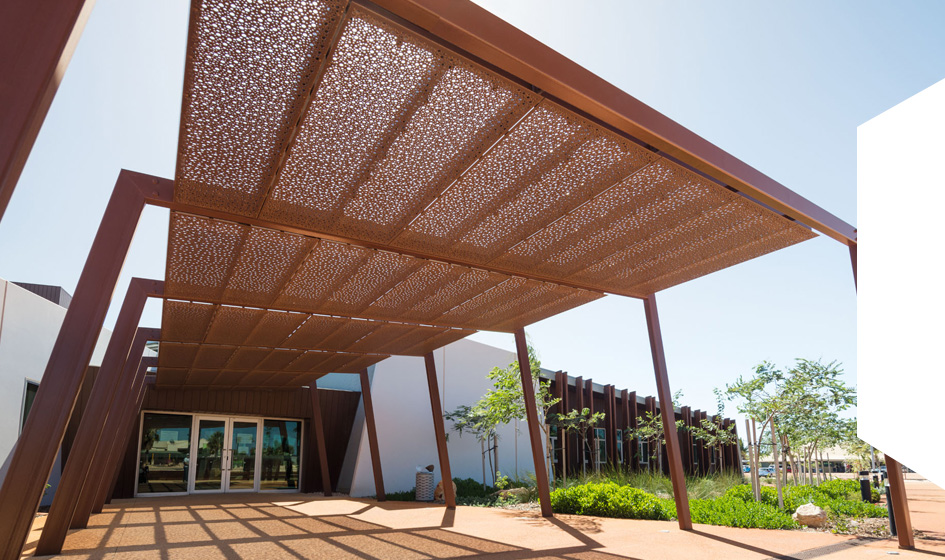
Ninglaoo Centre Exmouth – Atomic Pattern (PHOTO: John Gollings Photography)
Solutions Driven
Perforated metal is a form of sheet metal that has been punched or stamped with a machine to create a pattern of holes. It is also known as perforated sheet, perforated plate, or perforated screen and is commonly made from aluminium, cold rolled steel, stainless steel and many other decorative substrates including brass and copper.
The process of perforating metal has been around for over 150 years. Originally designed for the efficient separation of coal, the perforations were manually punched by hand. Increased demand has now seen that process developed beyond rotary pinned rollers, die and punch presses and right through to laser cutting.
WHO USES PERFORATED METAL?
Architecture
Chemical and energy
Filters, centrifuges, drying machine baskets, battery separator plates, water screens, gas purifiers, liquid gas burning tubes, mine cages, and coal washing
Food and beverage
Beehive construction, grain dryers, wine vats, fish farming, silo ventilation, sorting machines, fruit and vegetable juice presses, cheese molds, baking trays, and coffee screens
Automotive
Air filters, oil filters, silencer tubes, radiator grilles, running boards, flooring, motorcycle silencers, ventilation grids, and tractor engine ventilation
Construction
Ceiling noise protection, acoustic panels, stair treads, pipe guards, ventilation grilles, sun protection slats, facades, and sign boards
Material development
Glass reinforcement, cement slurry screens, dyeing machines, textile printers and felt mills, cinder screens, and blast furnace screens
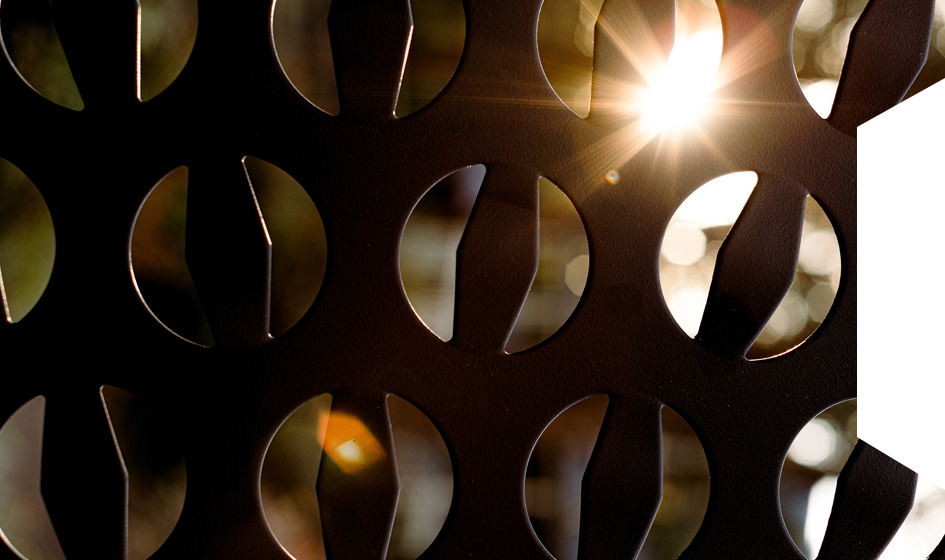
Form & Function
Light spill; airflow; shape, movement and intrigue – Metrix Group perforated metal products are a truly flexible solution, inside and out.